ElectroFin® Coatings
Thickness of Coating
Thin coatings are better for heat transfer, while thick coatings can lead to diminished heat transfer and restricted airflow over the condenser coil. It’s important to remember that when fin spacing on condenser coils gets denser, a thick coating can cause fin bridging to occur, which severely restricts the efficiency of a condensing unit.
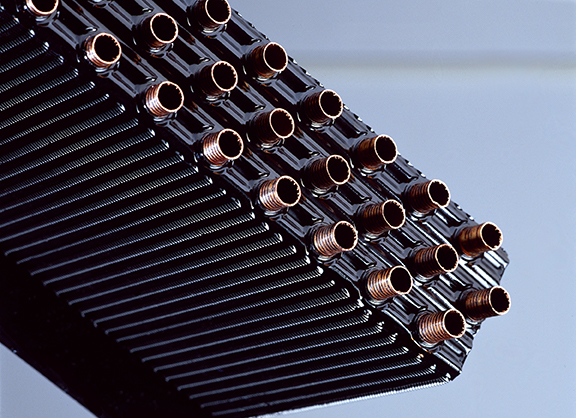
Flexibility and Impact Resistance
Flexibility and impact resistance: An inflexible or brittle coating will crack or flake when the coils get hit or bent, which is a normal occurrence. When even the smallest portion uncoated metal is exposed, the underlying metal will begin to corrode.
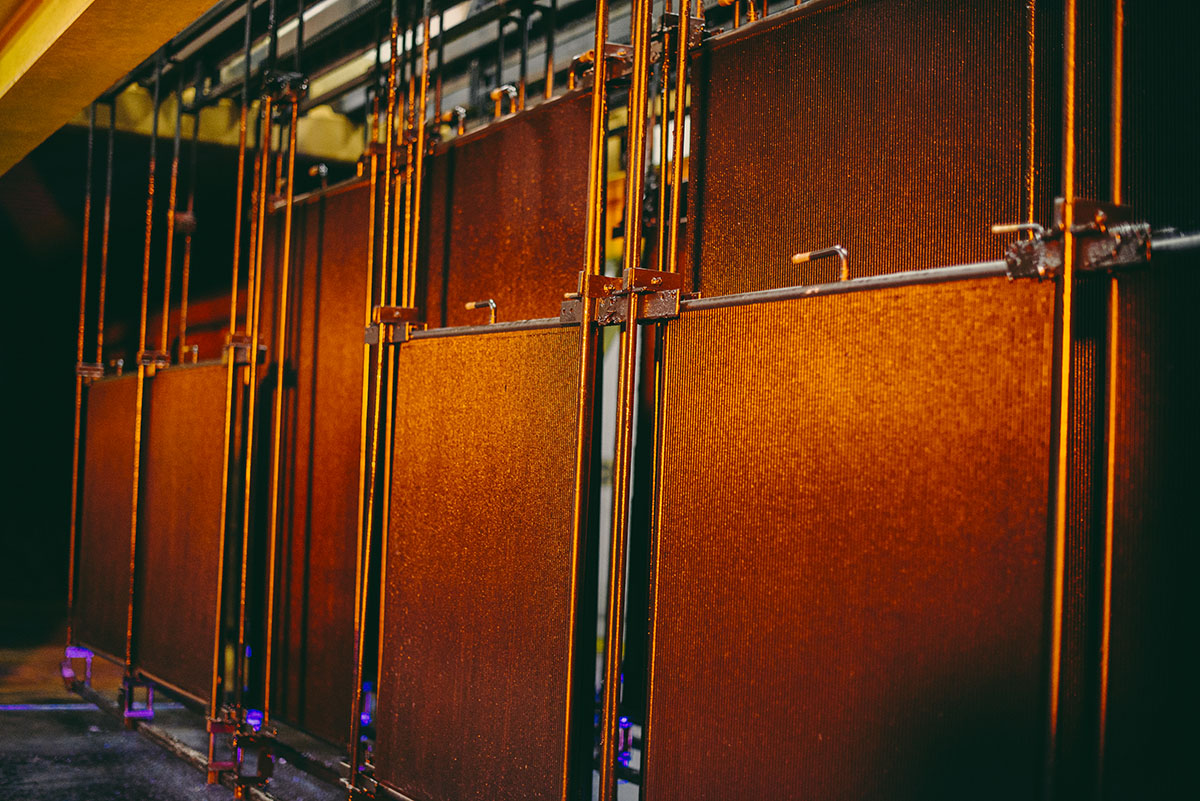
UV Resistance
Condenser coils that will be exposed to sunlight should have a coating that is resistant to UV radiation. Several of the popular post-coats do not have inherent UV resistance and offer polyurethane “topcoat” to prevent rapid deterioration of their base coating. Polyurethane is UV resistant; however, the extra layer of polyurethane adds undesirable thickness to the coating.
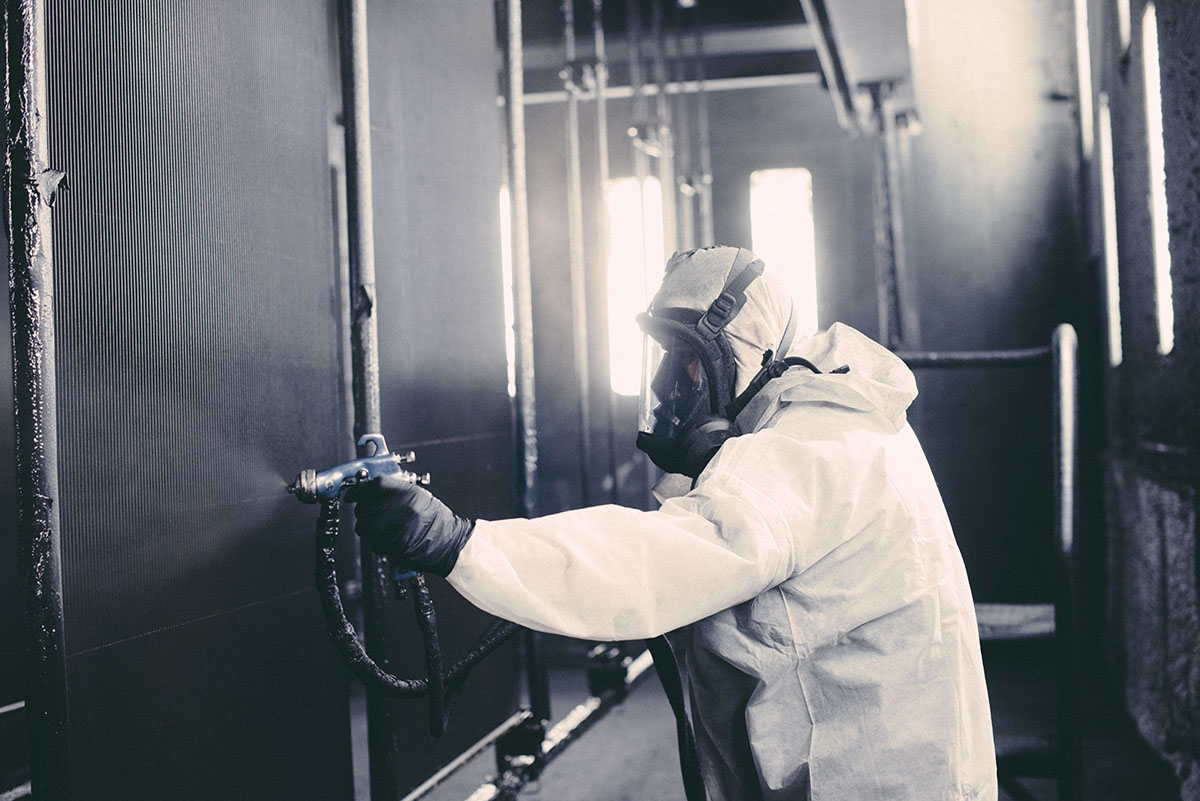
Coatings for Aluminum Microchannel
In recent years, the air conditioning industry has been striving to improve energy efficiencies and reduce cost. HVAC innovations include the all-aluminum micro-channel heat exchanger (MCHE), a technology used by the automotive industry for many decades. Benefits of MCHE include increased heat transfer and thermal performance, as well as the delivery of lower coil weights. Further, MCHE can reduce refrigerant charge by up to 85% and lower noise levels as a result of reduced fan speeds. With technological advancement comes challenges. MCHE is no exception, particularly when selected for installation in corrosive conditions. ElectroFin® E-Coat meets that challenge head on to extend useful service life.
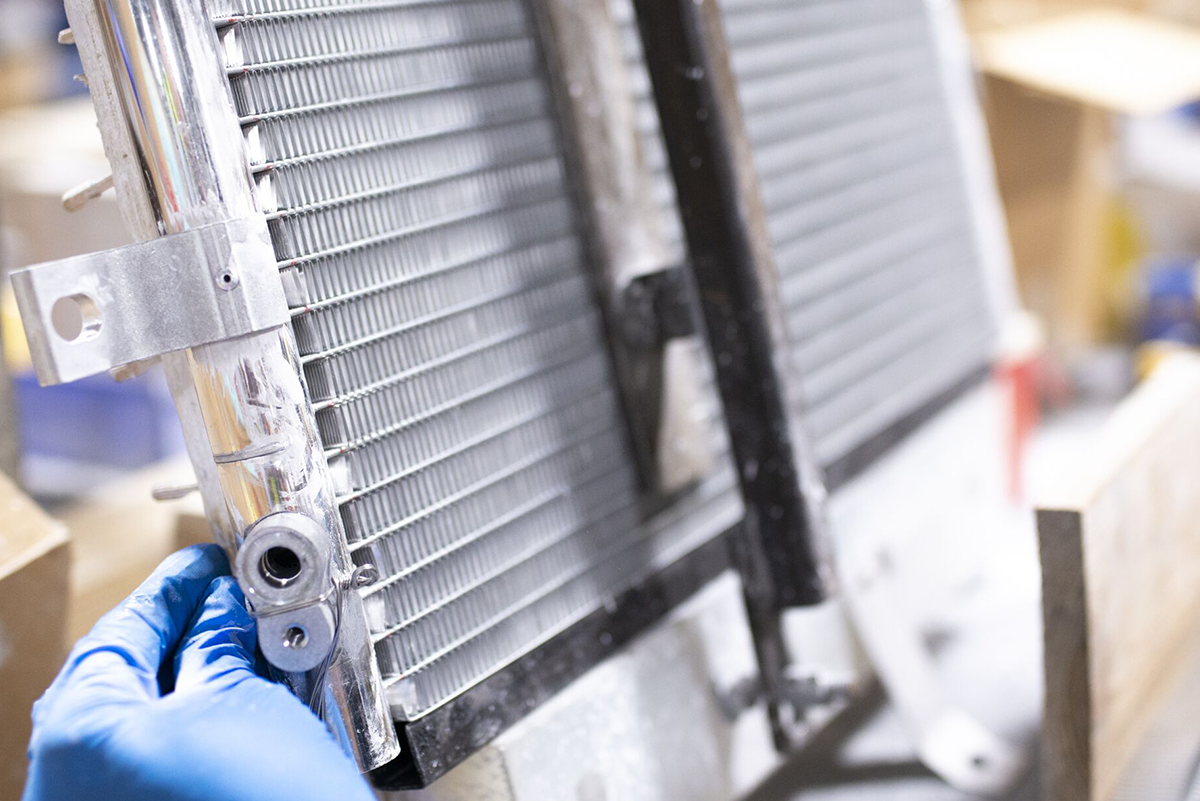
ElectroFin® E-Coat is used in many applications, including:
- HVAC Equipment
- Commercial Equipment
- Industrial Coils & Coolers
- Aerospace & Military Applications
Microchannel coil construction uses all aluminum alloys with brazed in construction. Regardless of metal type, when exposed to an environment, all metals will react to their environment. The rate of reaction is dependent on temperature, humidity, and pollution in combination with alloy (metal) selection. While MCHE’s all aluminum construction is more resistant than traditional round tube and plate heat exchangers, it is still not immune to corrosion, particularly when in the presence of chlorides or sulfides, which are typical in coastal and/or highly polluted areas. So, as with traditional heat exchangers, protection is needed. Coating coils designed with enhanced fins or high fin densities, without bridging, is a challenging endeavor.
As advancements in heat exchanger design brings us to smaller and more complicated surfaces, ElectroFin® has kept pace with the challenges of the latest technology. Working with the leading MCHE producers, we have studied the dynamics of proper pre-treatment and electro-coating for all-aluminum heat exchangers.
Both ElectroFin® Louiseville, KY and Jacksonville, TX plants are ITAR compliant. ElectroFin® E-Coat is available for all military applications where corrosion, light reflection or radar absorption can be a formidable factor. ElectroFin® E-Coat with high edge build technology can be
found on over a hundred thousand micro-channel condensers.