ElectroFin® E-Coat Process
ElectroFin® E-Coat developed a specific e-coat formulation to allow extension of e-coat protection to RTPF and MCHE technology. To assure proper coating coverage without bridging, ElectroFin® E-Coat with high edge build technology should be specified. ElectroFin® has successfully applied e-coat to hundreds of thousands of heat transfer coils which are in service globally; most are in extremely harsh environments.
The ElectroFin® E-Coat process begins with the customer in mind. When you specify ElectroFin® E-Coat as your protective coating, you are getting much more than just the very best in corrosion protection. We recognize you as the owner of this equipment, and we take on the responsibility of assurance that your equipment will be properly handled and managed throughout the e-coating process. Every job is unique and personal. We are not a factory – we are applying science, technology, and integrity to your property.
E-coating in general is a common process, but ElectroFin® E-Coat is unlike all others. The engineers at ElectroFin® took an existing technology and reapplied it to specifically meet the needs of today’s advanced HVAC/R heat transfer coils. Our process is optimized to apply the most complete coverage throughout the coil, while assuring that the applied coating is uniformly micro thin, yet hard and flexible. As we have mentioned, ElectroFin® E-Coat is exclusive for heat transfer coils only. No other products will infiltrate or contaminate our process tanks.
The ElectroFin® E-coat process begins at the receiving dock:
Units that arrive at ElectroFin® undergo a complete inspection for damages of the fins and any residues that may prohibit the e-coat process from surface adhesion. All units received and approved for production are labeled with an identification tag that will remain with the unit throughout the coating process, as well as the unit’s lifespan. This ID number can trace every step of the ElectroFin® E-Coat process and support your the coating’s 5-year warranty. The ID number also helps ElectroFin® to locate your original unit carton packaging, so that when the unit is complete, your original container is aligned with your coil.
1. All portals, tubes, and inlets are covered or masked off to prohibit any e-coat or rinsing chemicals to enter the system. If the unit arrives with a gas charge, the charge is depleted. This will be refilled at the end before final packaging.
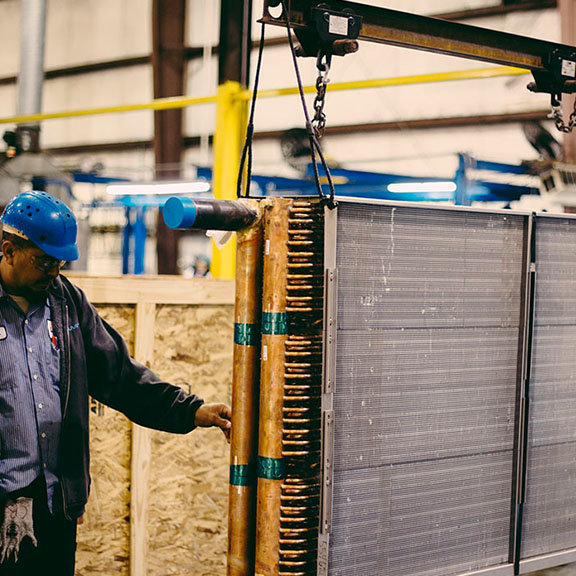
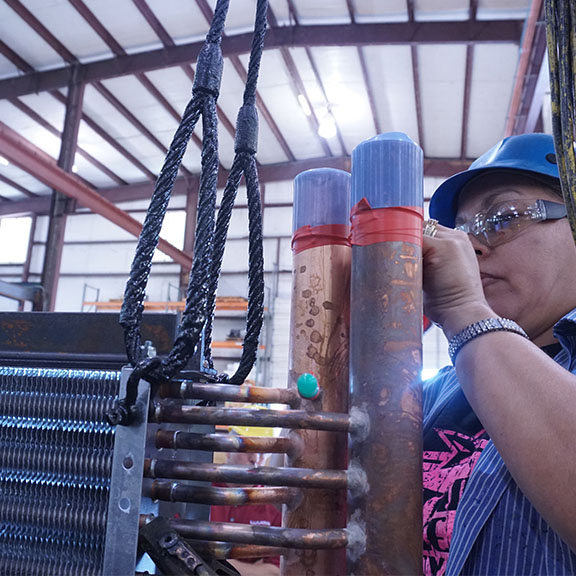
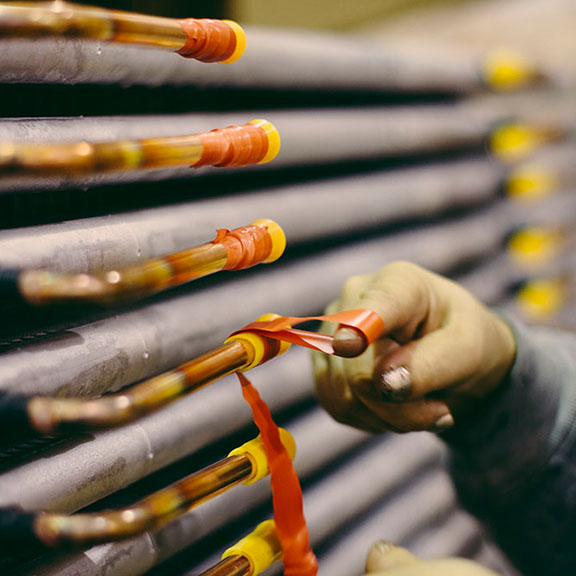
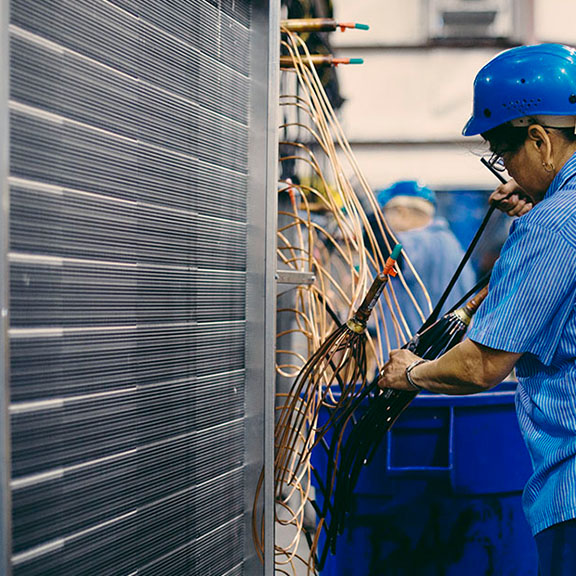
2. The unit is loaded to our overhead crane on a load bar that is specific to each coil coating job, and is then prepared for the first tank – a washing process. During this step, the coils are cleaned with an alkaline cleaner to remove dirt and oils. Typically, units from the OEM will arrive with dust, dirt particles, residue, and metal deposits derived from factory conditions and transportation.
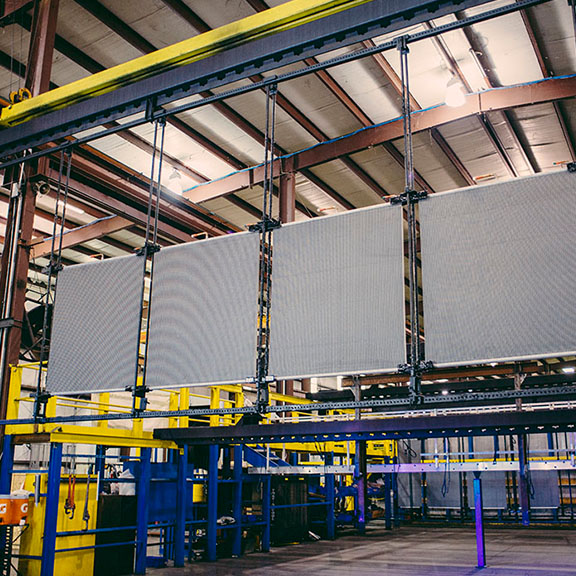
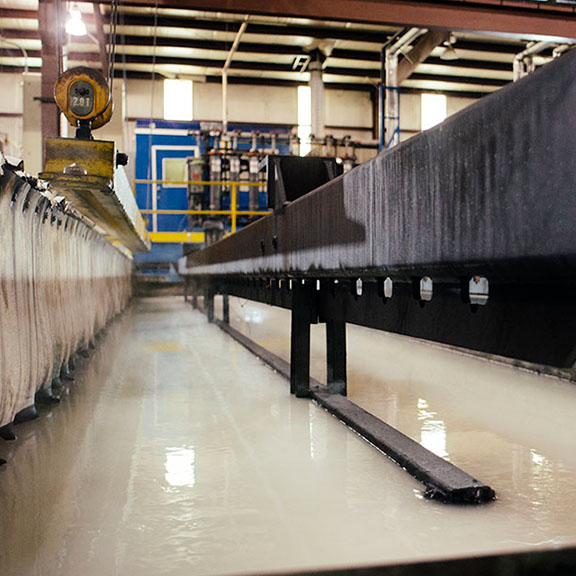
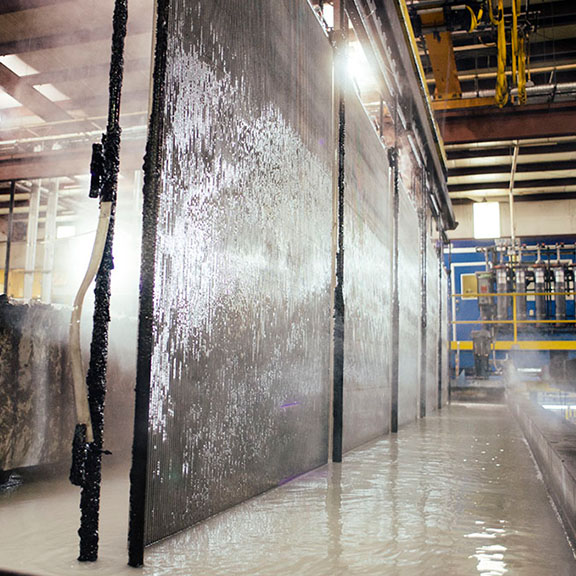
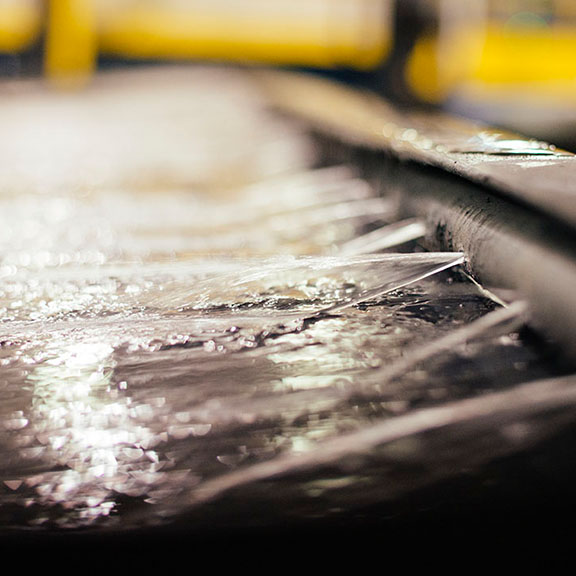
Note: This step is exclusive to ElectroFin® and is crucial to ensuring a clean application of the e-coat surface. Pretreatment, a critical step, ensures reliable bonding of the metal and coating later on in the process. You will not get this in any spray field application.
3. The part is then channeled through a two staged rinsing process – a heated first stage followed by an ambient second stage prior to entering the e-coat tank.
4. The ElectroFin® E-Coat process is proprietary. The unit grounding process is unique to ElectroFin® and ensures complete coverage of the coil. Upon entering the e-coat tank, the paint bath is a mix of 80% water and 20% POWERCRON® paint. Electrically charged paint particles carry a positive charge and are attracted to the negative grounded metal surfaces. The ElectroFin® E-Coat process is computer controlled. Through our computer system, our operators can visually detect any areas that are not covered, ensuring that we can completely cover the coil. ElectroFin® E-Coat is the only process that guarantees complete coverage throughout the unit. There is no external surface area that is not completely covered and protected.
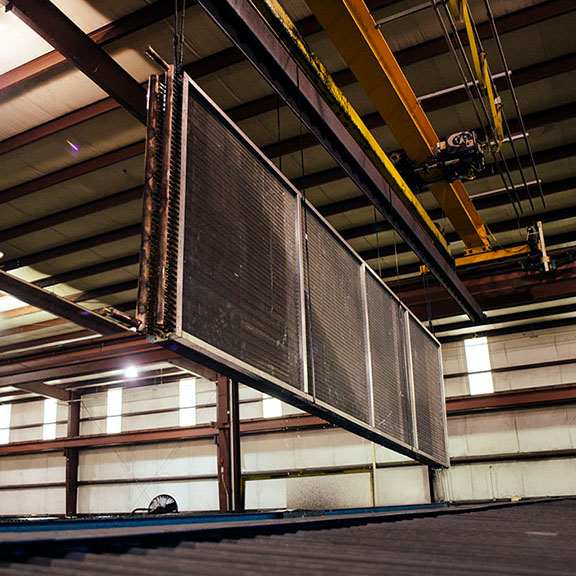
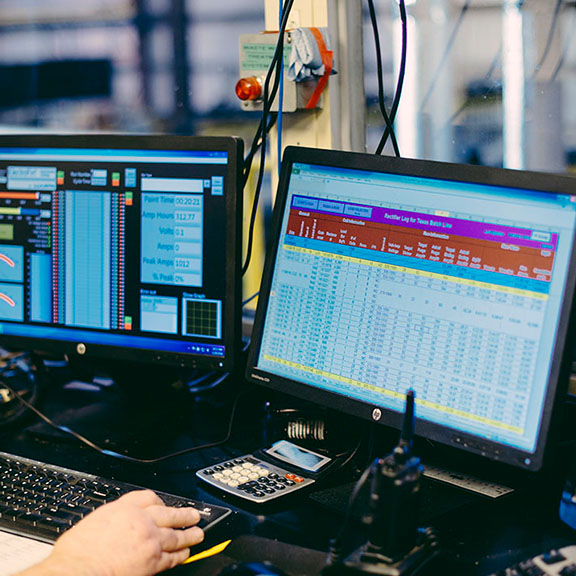
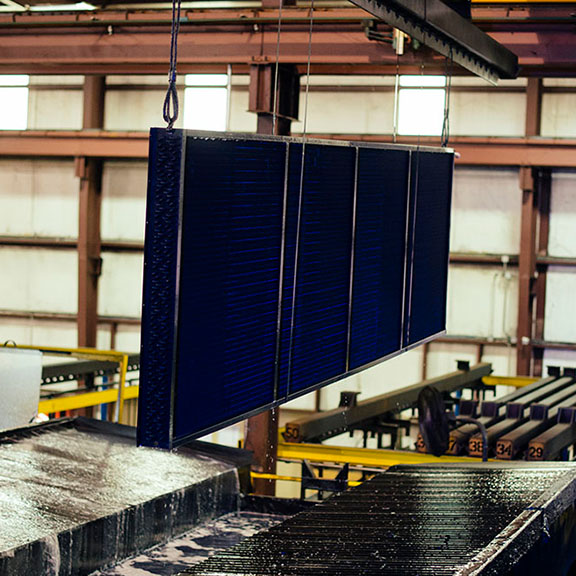
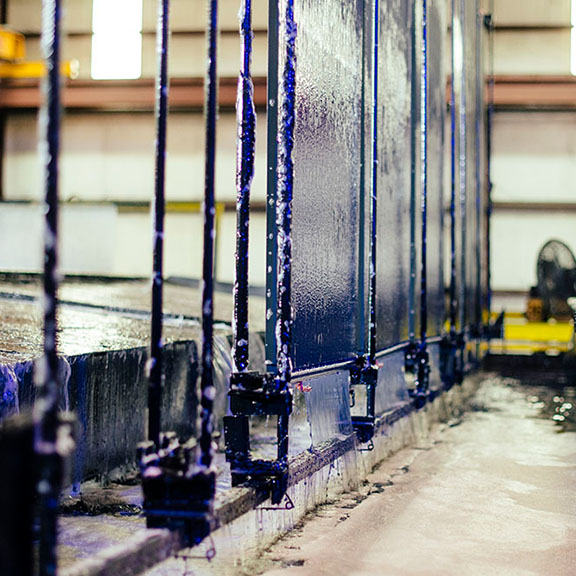
5. Upon removal from the e-coat bath tank, the unit is visually inspected and moved to a final rinse tank where the unit is spray rinsed to remove any loose paint particles.
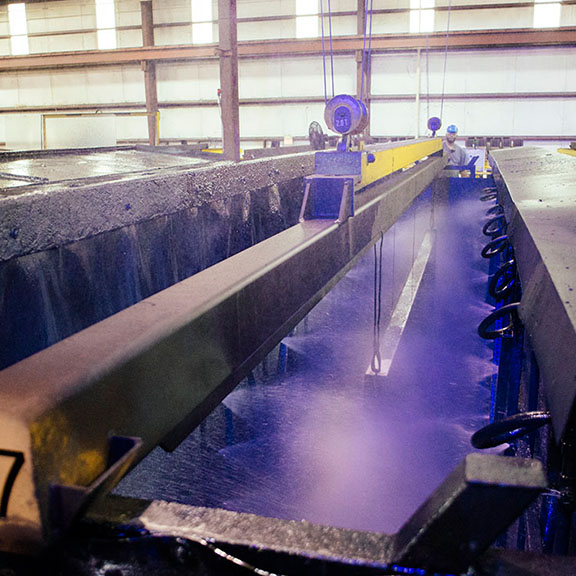
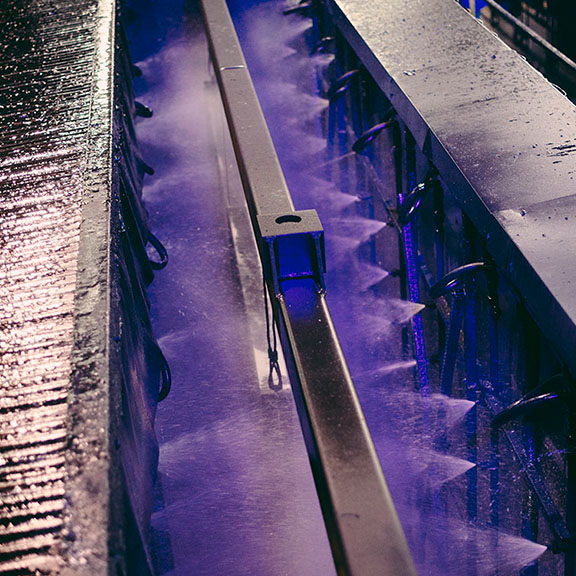
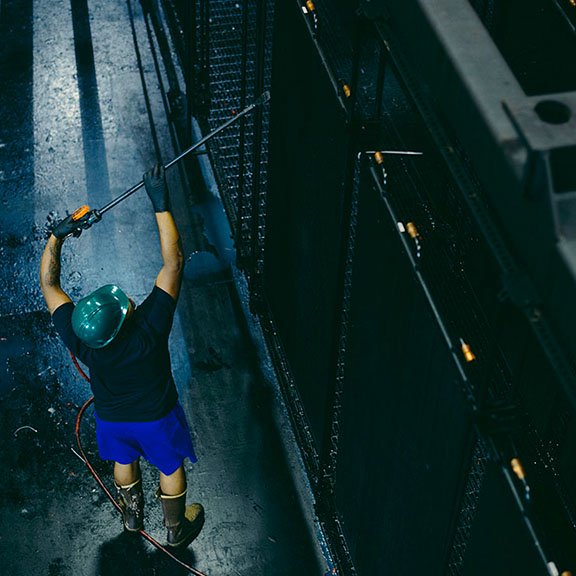
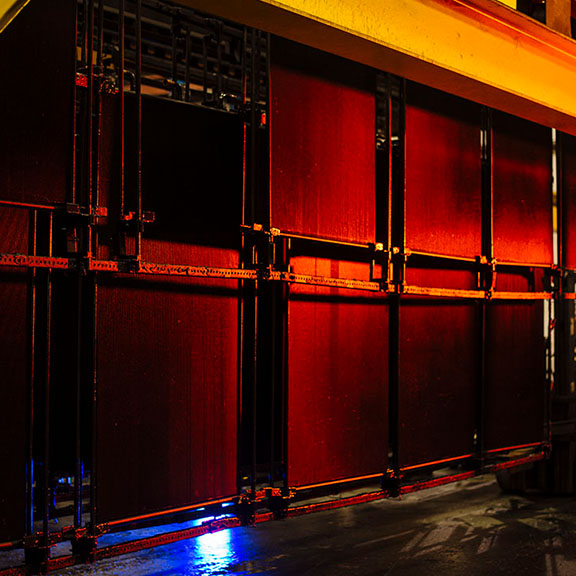
6. The unit is now ready for the coat curing process in our drying chamber. The drying chamber gradually reaches its optimal temperature, and then the unit will cool before removal. The entire process takes several hours. The curing process creates a smooth, hard shell designed to resist corrosion, pitting, and flaking. The drying chamber crosslinks and cures paint resin film, resulting in a high quality finish without runs, drips, and sags.
The ElectroFin® E-Coat surface is micro thin to allow for maximum air flow without diminishing the engineered efficiency of the unit. This extremely durable and flexible film covers the entire copper tube aluminum fin coil surface, and includes cavities and recesses areas.
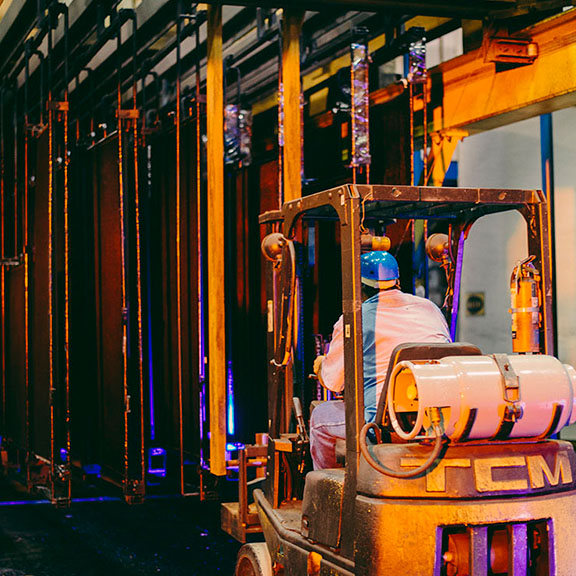
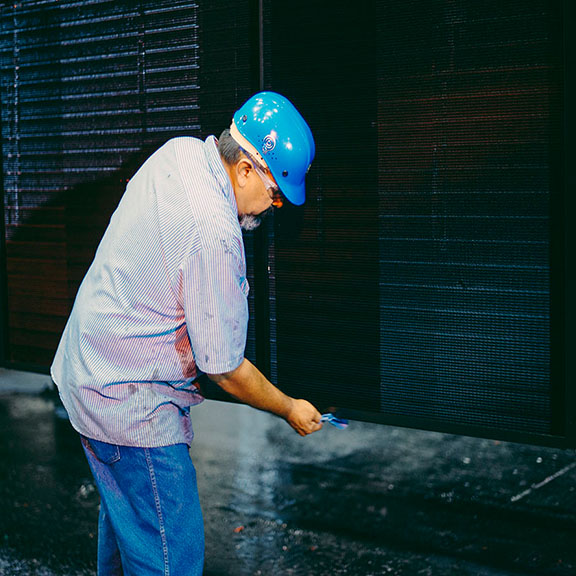
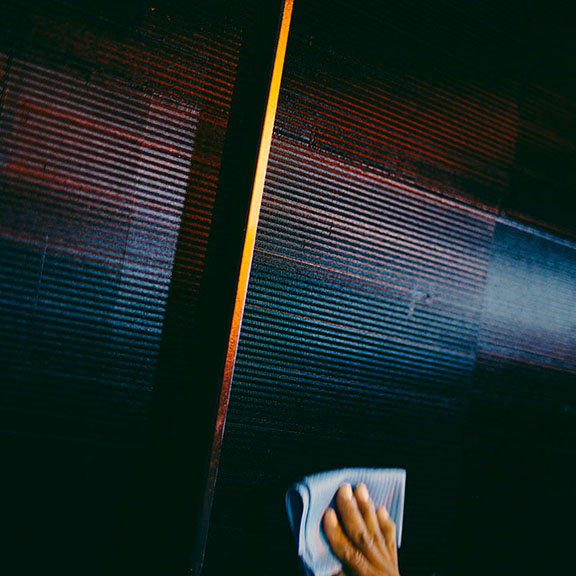
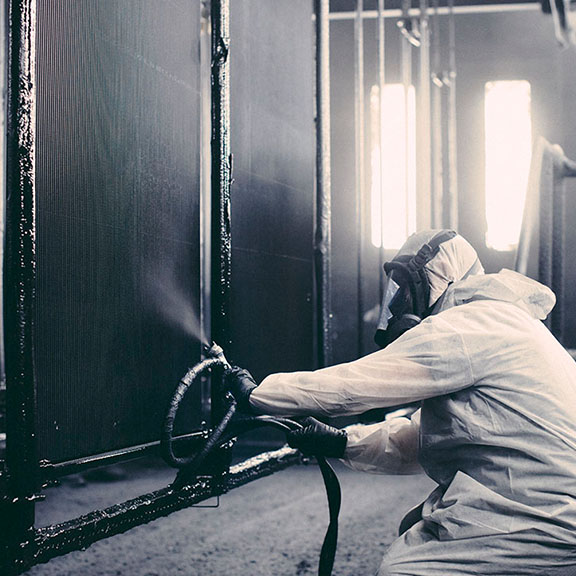
7. When the coil curing process is complete, an inspection is performed to ensure that all e-coating is cured and dry. Units are then staged for optional UV Top Coating. The UV Top Coat is manually applied using a spray gun and booth and will help to resist the fading effects of direct sunlight on the e-coat application. Attention to application of the spray is taken by the operator to ensure a uniform coat.
8. From here, the ElectroFin® E-Coat coils are given a final inspection (for any bent fins or debris) and aligned with the original packaging. All masking or capping materials are removed and units requiring a holding charge are re-pressurized. The unit is repackaged and returned to the OEM for incorporation into the final unit.
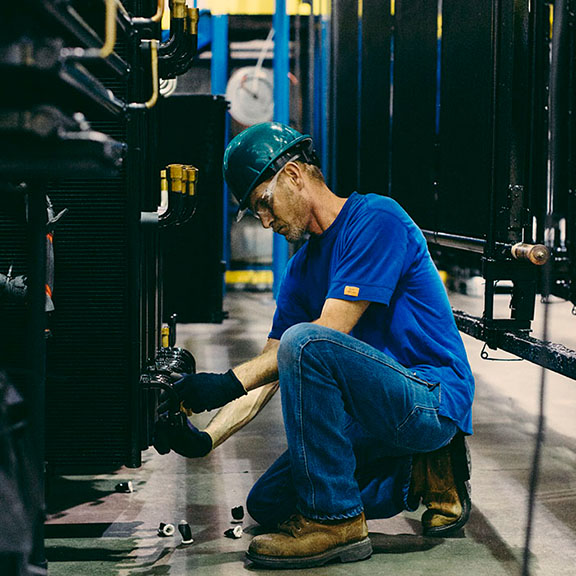
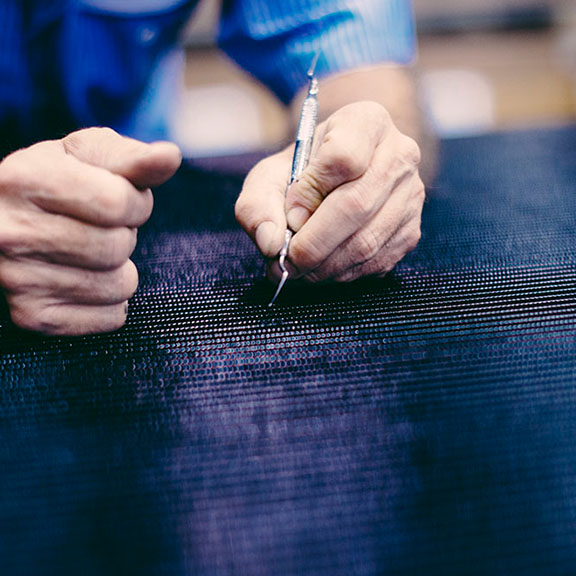
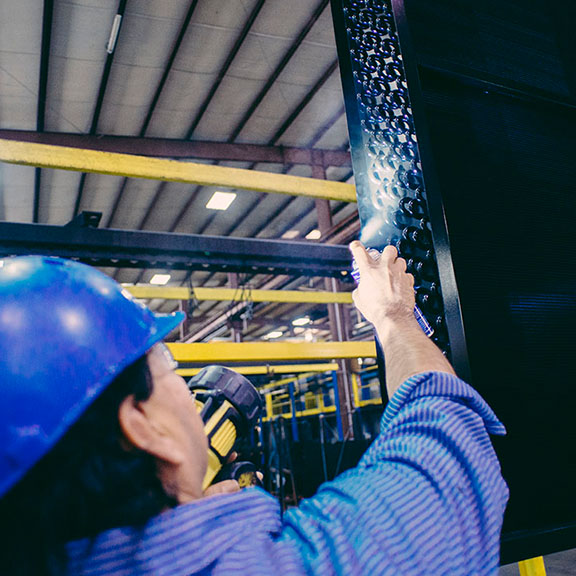
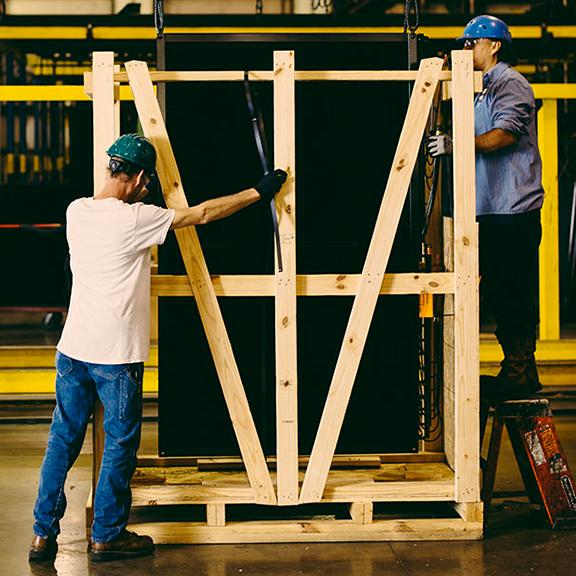
The ElectroFin® E-coat process takes about 5 days (start to finish), not including the time allowed for transporting to and from our plant facilities. ElectroFin® supports this unit and its customer with a five (5)-year warranty on coating and workmanship. Few, if any, other e-coating or spray applicators provide this type of product assurance. When comparing protective coatings, look for the longest warranty available. ElectroFin® E-Coat is warranted to be free of defects in materials and workmanship for five (5) years, provided that coils and components are properly and routinely maintained, and records demonstrate proper cleaning procedures and approved products were used.
ElectroFin® E-Coat is the premiere brand in the HVAC/R industry and offers the highest level of corrosion protection available from an electro coating provider.
ElectroFin® E-Coat is an internationally recognized e-coating process that has been reapplied by our engineers and redesigned to provide the ultimate protection for condenser and evaporator coils.
ElectroFin® E-Coat is ideally suited for coastal and offshore environments as well as industrial areas with high humidity and aggressive atmospheres, such as electrical power plants, refineries, waste water treatment plants, and urban areas with nearly permanent condensation and high pollution. ElectroFin® E-Coat extends the lives of HVAC/R heat transfer coils and components, reduces maintenance and operating costs, and is used by every major OEM.
There are two basic types of electro coating processes – Anodic and Cathodic systems. An Anodic system deposits a negatively charged polymer onto a positively charged part. With a Cathodic system, the reverse is true. The ElectroFin® E-Coating Process is a Cathodic system using electrical energy to deposit an epoxy coating to the heat transfer coils.
The ElectroFin® system uses PPG POWERCRON® Cathodic epoxy coating. This amazing product is superior in salt, chemical, and humidity corrosion resistance, and is the benchmark for all those that follow. POWERCRON® provides excellent edge coverage of fins, as well as uniformity of coverage and coating thickness. This unique polymer controls the flow characteristics of the coating, and can provide 100% coil coverage without bridging between fins. It is internationally recognized as the best corrosion protection for fin and tube and microchannel heat exchangers in coastal environments.
Other coating processes involving manual dipping or spraying can create surface imperfections, varying and improper thicknesses, bridging between fins, or can leave behind microscopic holes that allow salt air or other corrosives to reach the metal. These results compromise performance and service life. Manual coating is also susceptible to coverage variances from one component to the next.